How to speed up your research and move from design hypothesis to characterization within days
Material development typically occurs on a 15–25-year horizon, sometimes requiring synthesis and characterization of millions of samples. Only for the development of new electrocatalysts, millions of new materials need to be screened in the next decade. If you extrapolate this to materials for solar cells, batteries, thermoelectric materials and materials subject to supply disruptions, like rare earth metals, it is clear that this will be putting huge pressure on material researchers in the coming years.
Nanoscale offers a whole new range of possibilities for the discovery of new materials with improved properties. But it is impossible to accelerate material discovery without a solution to produce small nanoparticles at large scale and with consistently high quality.
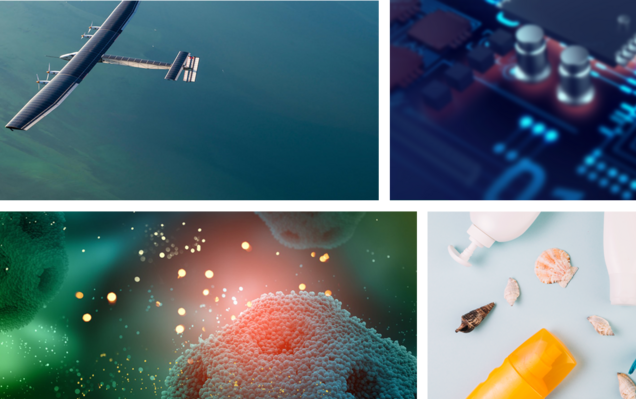
Scientists and companies that are developing the next generation of materials today, all require in-house industrial nanotools to produce nanomaterial tomorrow. Existing methods to produce smaller than 20 nanometres nanoparticles are not scalable as they all need dedicated infrastructure and are very labour intensive. They also suffer from low reproducibility (batch to batch variations) and limited size and composition control. Furthermore, the material versatility is an issue.
Considering that usually a lot of design hypothesis need to be tested before materials with certain properties are successfully synthesized, it is essential that the steps and required time of each iteration are significantly reduced.
An example of existing nanoparticle synthesis method that illustrates those arguments is wet chemical synthesis. Until today, wet chemical synthesis methods have been widely used for the preparation of nanoscale materials and they are considered very promising techniques towards high yields. However, most of wet chemical synthesis routes require a lot of time and effort.
Moving from the design hypothesis to the characterization of the produced sample requires a lot of steps, iterations and waiting time. Because the process is not automated, human errors and impurities originating either from the supplied chemicals or the insufficient removal of solvent/surfactants lead to substantial variations between different batches, as well as uncertainty on what might have been the problem during synthesis.
Nanoparticle synthesis takes places in the gas-phase and is a fully automated process based on spark ablation technology. The only requirements are power, (inert) gas and a pair of electrodes of the desired material/composition. The produced nanoaerosol can then be directly deposited on the desired substrate by using different VSP-A Series Accessories. Due to automation and the fact that there are no chemicals or surfactants required, the produced samples are reproducible and free of contaminants. At the same time, the yield of the process is high (order of mg/h) compared to other gas-phase synthesis methods and it is based on a scalable principle, which means that even industrial applications could be possible soon.
In practical terms, thanks to our innovation the discovery phase of novel nanomaterials is reduced from months (as it is today) to days. At the push of a button, in an easy, safe and reproducible way.
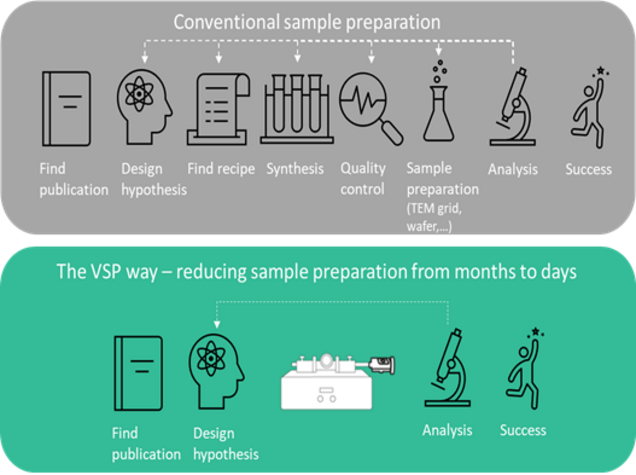
VSPARTICLE offers the solution to those exact problems, enabling researchers to work faster and move from design hypothesis to characterization within days.
VSPARTICLE addresses the challenges by offering a fully automated nanomaterial fabrication process based purely on a physical process. Our approach is radically different from the state-of-the-art and it is based on a patented technology called Spark Ablation. The cornerstone of our technology is the VSP-G1- Nanoparticle Generator.
What used to take months of complex material development work can now, with the help of VSPARTICLE technology, be done in days.
VSPARTICLE addresses the challenges by offering a fully automated nanomaterial fabrication process based purely on a physical process. Our approach is radically different from the state-of-the-art and it is based on a patented technology called Spark Ablation. The cornerstone of our technology is the VSP-G1- Nanoparticle Generator.
The VSP-G1 Nanoparticle Generator is a table-top, user-friendly nano-material generator. Thanks to this device, producing the desired nanoparticles becomes as easy as pushing a button: users simply select the size and wait for their sample to be ready. The typical sample preparation time is between 30 and 60 minutes. This device is compatible with any (semi-)conductive material (alloy and non-alloy).
With the VSP-G1 Nanoparticle Generator, a stable and clean flow of well-defined pure nanoparticles can be generated, without the use of precursors and surfactants. The produced nanomaterials can be directly incorporated into a next process step, or even directly in a product.
The uniqueness of our technology lies in the combination of predictability, accuracy and automation. The technology is material agnostic, making it applicable for many applications and markets. The VSP-G1 Nanoparticle Generator provides you with the possibility to perform ground-breaking research within the field of nanomaterials, avoiding the limitations of common generation methods and materials. It allows you to move through the research cycle quickly, fast forwarding from hypothesis to success.

Comments
No Comments