Industrial tools
Since its founding in 2014, VSParticle goal has been to go beyond the research market and supply tools for mass production.
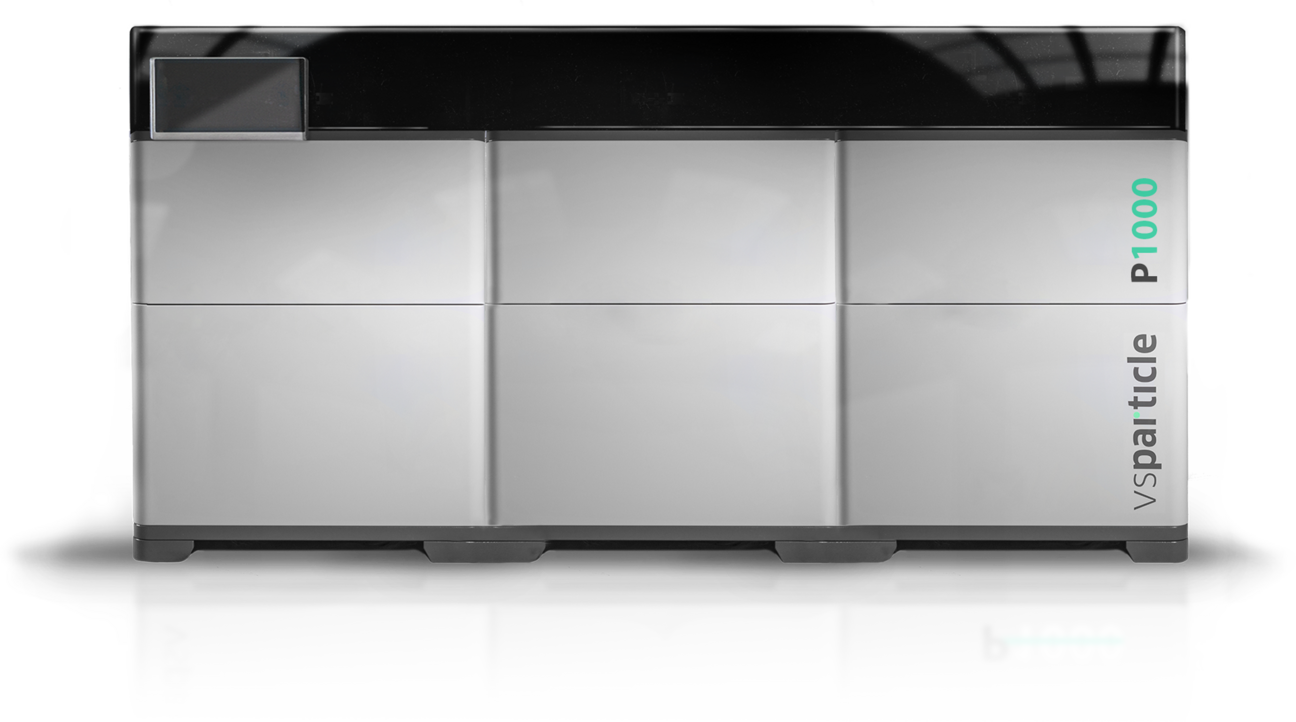
From research to mass productions
VSParticle is accelerating the discovery and development of high-performance thin-film nanoporous catalyst layers—a critical component in electrolyser stacks essential for unlocking the full potential of green hydrogen.
With a clear roadmap toward gigawatt (GW)-scale deployment, VSParticle is advancing a sustainable, efficient, and automated technology platform designed for industrial-scale green hydrogen production.
Since 2017, VSParticle has provided cutting-edge R&D tools to leading universities, research institutes, and corporate innovation centers. In 2023, the company launched its most advanced research tool (VSP-P1 Nanoprinter) specifically developed to accelerate material discovery through rapid, reproducible deposition of thin-film nanoporous layers.
Supporting all stages of material development
With its advanced nanoporous thin-film manufacturing platform, VSParticle supports the entire ecosystem of material innovation:
- Researchers and innovators who are developing next-generation electrolyser materials to improve performance and durability. The VSP-P1 serves as the foundation for self-driving labs, capable of screening materials 100x faster than traditional R&D workflows.
- Industrial stack manufacturers who are seeking next generation Porous Transport Electrodes (PTE) for PEM water electrolysis with 90% less Iridium than today.
VSParticle supports their customers with new synthesis tools or material synthesis service. Our disruptive approach will stimulate green hydrogen production and accelerate the progress for a clean and sustainable energy future.
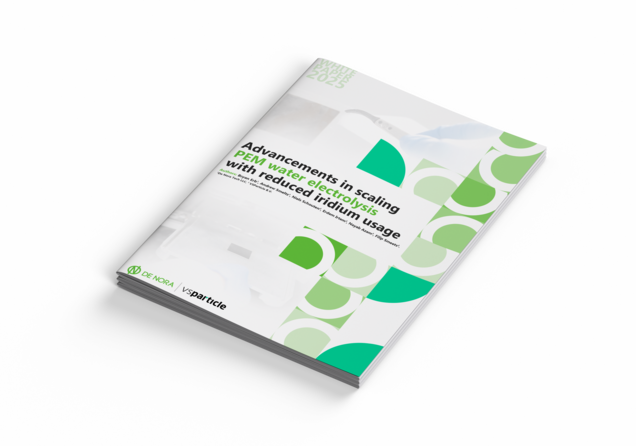
White paper
Advancements in scaling PEM water electrolysis with reduced iridium usage
This paper outlines the potential to reduce iridium loading below 0.1 mg/cm², making PEM electrolysis significantly more scalable and sustainable.
Technology scaling roadmap
In the overview below, you could see how we will move from research to development and production tools by first increasing the output (moving from VSP-G1 Nanoparticle Generator to next generation VSP-G100) and then numbering up in a second step.
Research Tool
To accelerate material screening, the Research Tool (VSP-P1 Nanoprinter) is designed with flexibility in mind. Flexibility regarding the materials that can be processed and the type of substrates.
This new way of additive manufacturing can greatly simplify the production of nanoporous thin films and layers with a high surface-to-volume ratio. The applications of such films are numerous and include for example electrocatalysis, gas sensors as well as the fabrication of batteries and microelectronics.
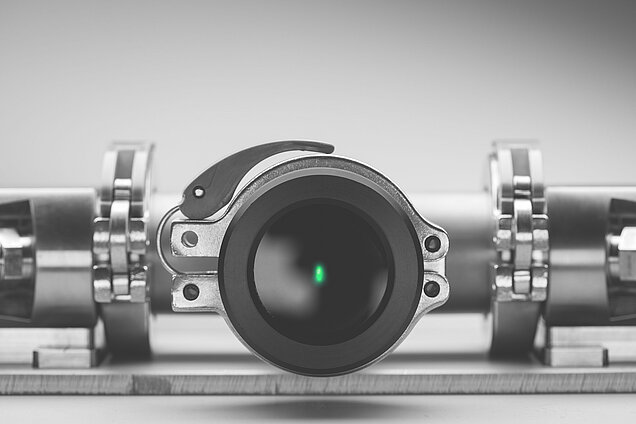
Blog
Spark ablation for nanoporous material production
Discover how nanoprinting technology efficiently fabricates high-quality materials and how AI-driven combinatorial material discovery accelerates innovation across diverse industries.
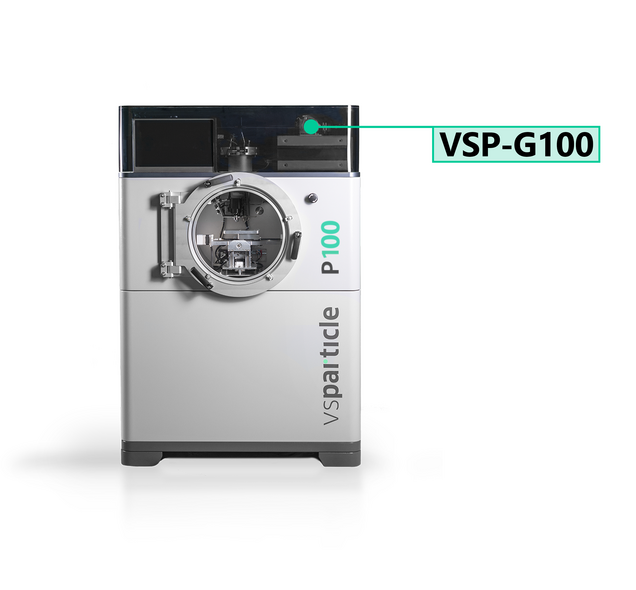
Process Development Tool
When the desired material is discovered, the printing process needs to be optimised for production. This can be done on the Process Development Tool (PDT) equipped with the next-generation VSP-G100 Nanoparticle Generator. This new tool is designed to increase mass output by 100x compared to the VSP-G1. This boost in production capacity is accomplished by increasing the electrical sparks frequency that generates a certain number of nanoparticles. With a target of 25,000 sparks per second, the PDT is set to reach a printing speed 100x faster than current models operating at 300-500 sparks per second. After the process has been optimized for yield and material performance, it is time to prepare for production.
VSParticle introduces catalyst layers for PTEs and catalyst loading is reduced without compromising performance or durability.
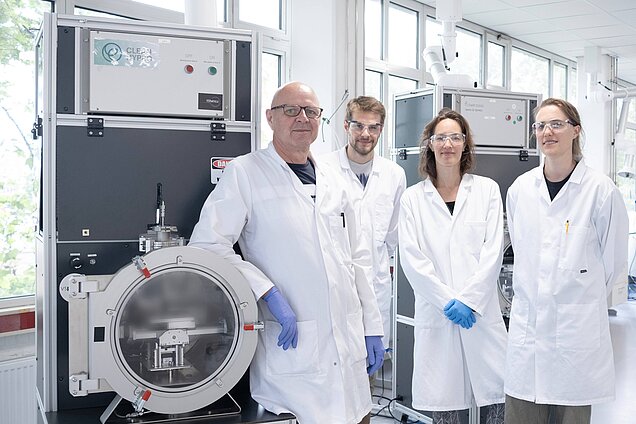
Blog
Revolutionizing PEM Electrolysers
Learn how VSParticle's technology reduces reliance on iridium by up to tenfold by optimizing electrocatalysts for
Production Tool
VSParticle’s scaling strategy emphasizes “numbering up” individual VSP-G100 modules, providing a streamlined expansion approach that preserves nanoporous material properties across different scales. Therefore, in the next phase, VSParticle will develop a High Volume Production Tool (HVPT), incorporating at least 10 particle generators to achieve technological maturity for industrial-scale nanoporous material production.
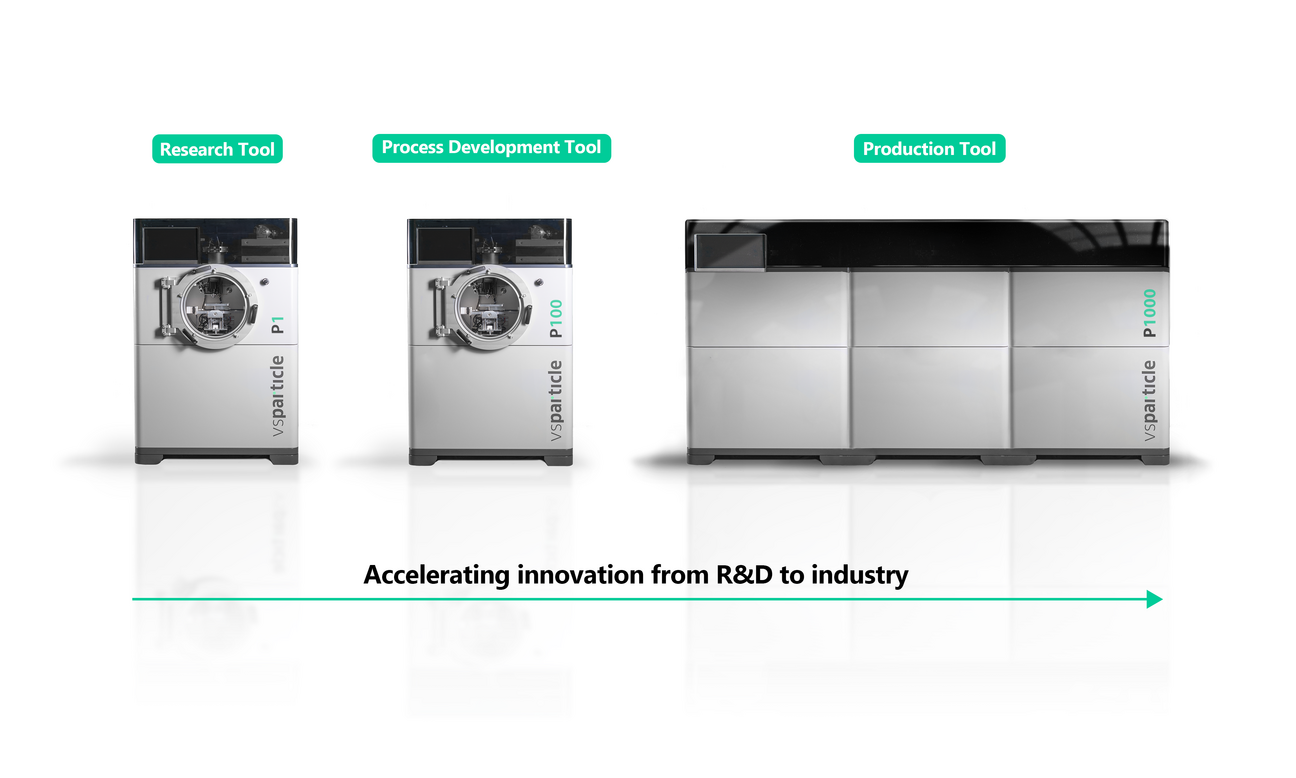