Catalyst Coated Membrane (CCM)
Boosting green hydrogen production through high-performing nanoporous Iridium coatings.
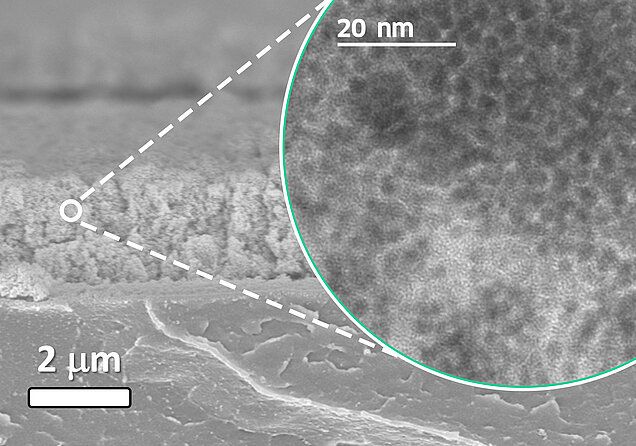
Cross section of IrOx coating on Nafion membrane, applied with the VSP-P1 nanoprinter (TEM) Zoomed-in section shows nanoporous IrOx material with high surface to volume ratio (SEM)
Source: Dutch Institute for Fundamental Energy Research (DIFFER), Catalysts | Free Full-Text | Spark Ablation for the Fabrication of PEM Water Electrolysis Catalyst-Coated Membranes (mdpi.com)
Proton Exchange Membrane Water Electrolysis and Anion Exchange Membrane electrolysis are emerging key technologies for the transition towards green hydrogen. Core element in the electrolyser-stack is the catalyst coated membrane (CCM), which is coated with Iridium.
High cost and scarcity of Iridium hamper the scale-up and cost-effectiveness of green hydrogen production.
The nanoporous layers made with VSParticle technology provide high performance CCMs, while Iridium loadings are substantially reduced.
Reducing Iridium loading in high performing CCMs
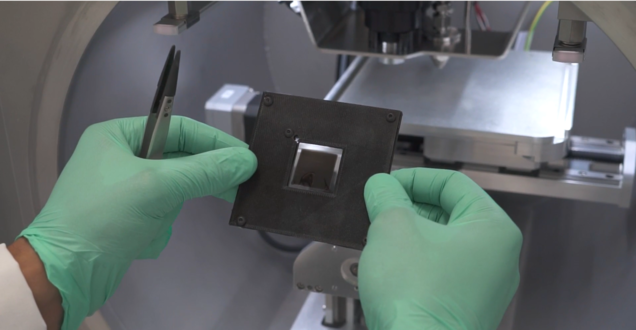
Development of efficient catalyst coated membranes (CCMs) is crucial for the transition towards a hydrogen-based, low carbon economy. Conventional CCM production processes require multiple steps and high loadings of scarce metals. By using pure bulk materials as a source and combining spark ablation with 3D printing (additive manufacturing), VSParticle can simplify the production process of CCMs, and catalyst loading can be reduced without compromising performance or durability.
Development of high performing catalyst coated membranes for PEM water electrolysis
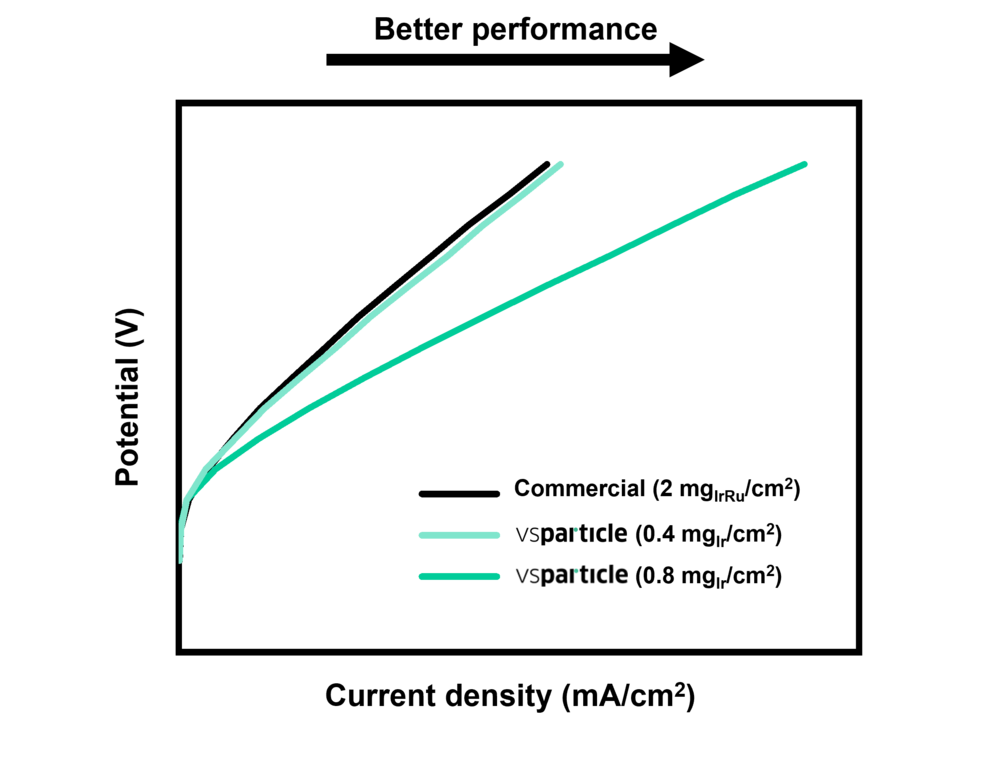
PEM water electrolysis is one of the applications that has gained lot of interest recently.However, market penetration is hindered because PEM water electrolysers rely on the use of scarce and expensive noble metal catalysts, such as Iridium. As a solution to this challenge, Iridium catalyst coated membranes were developed using VSPARTICLE technology and tested by an external party in a single-cell PEM water electrolyser. Results proved that less catalyst loading was required, compared to commercially available standard. More specifically, the Ir-specific power density was reduced up to an order of magnitude and durability was good based on three different degradation protocols.
Check out our solutions
VSParticle has introduced a range of new to the world products for the synthesis and deposition of conducting and semiconducting nanomaterials. While the VSP-G1 can be used as a stand-alone nanoparticle generator, the VSP-P1 is a nanoprinter, with an integrated VSP-G1 generator. The technology is scalable and next generations of nanoprinters for volume production are under development
Key benefits of VSParticle technology
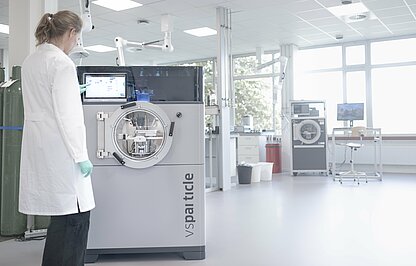
Accelerating the development of next generation CCMs
By combining spark ablation, a vapor-based nanoparticle synthesis method, with additive manufacturing, production process of CCMs is simplified and catalyst loading is reduced without compromising performance or durability.
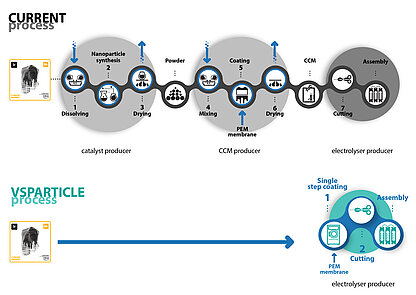
Eliminating 85% of the current production steps
Conventional CCM manufacturing processes are primarily ink-based and therefore require multiple steps for the material synthesis and coating process. Using our approach the nanoparticle synthesis and deposition process only requires one integrated step.
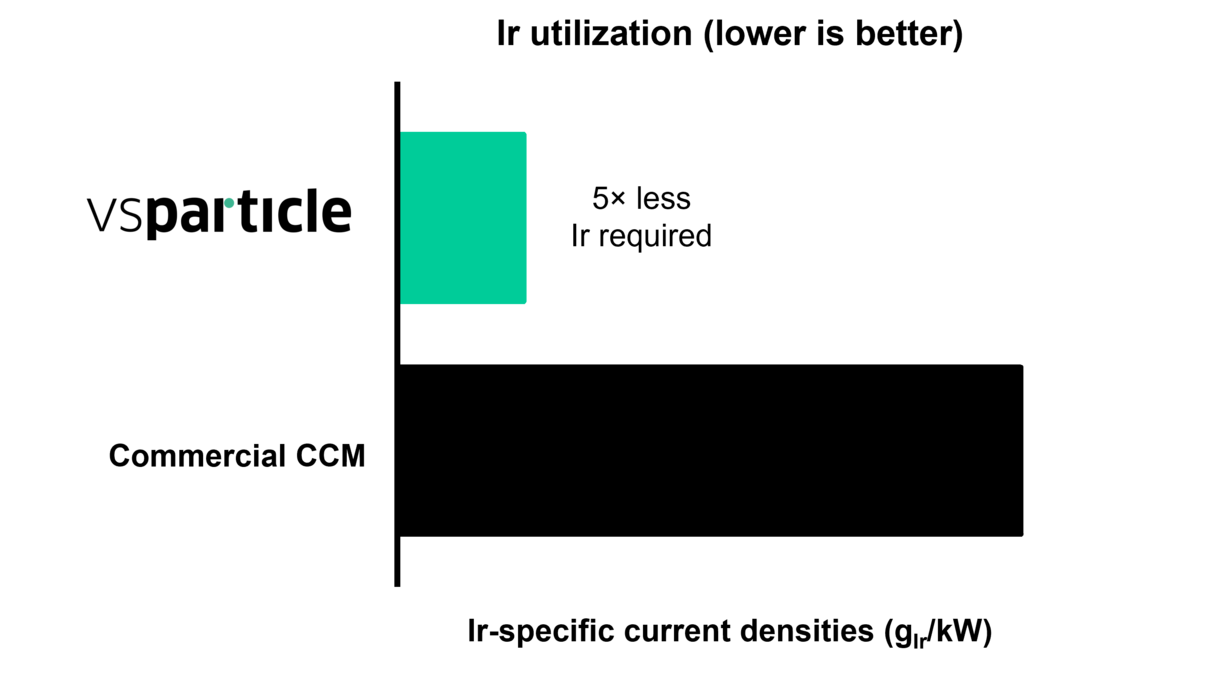
Enabling high performing CCMs
PEM water electrolysis test results have shown that Mbrane-produced CCMs had better activity with less iridium content compared to the commercial standard. Ir-specific power density was decreased by up to an order of magnitude.
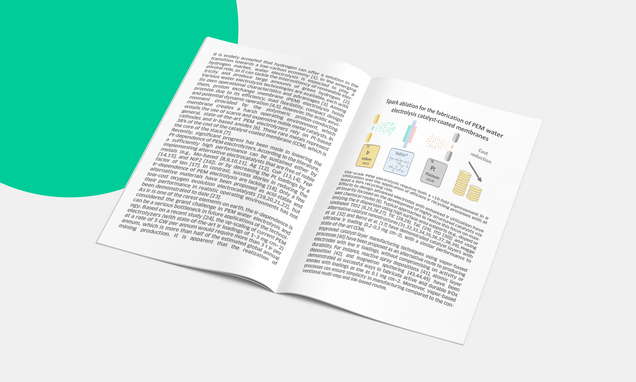
Publications
Spark Ablation for the Fabrication of PEM Water Electrolysis Catalyst-Coated Membranes