Clients:
Dr. Joost van Ginkel | TU Delft Alumni, Department of Microelectronics
Research Field: Advanced sensor materials, MEMS Technology, Micro/Nano System Integration and Reliability
Research tool:
VSP-G1 Nanoparticle Generator and prototype of Nanoprinter (P0)
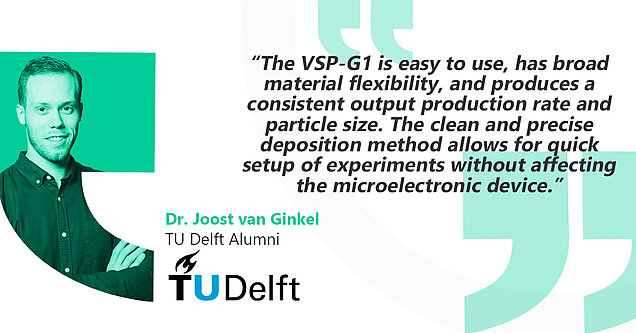
Dr. van Ginkel, could you briefly introduce yourself and explain how your educational expertise aligns with your research focus involving the VSP-G1 and P0 prototype?
I have worked closely with VSPARTICLE for the past six years, starting as their first intern during my MSc Chemical Engineering internship. For my MSc thesis project, I collaborated with Andreas Schmidt-Ott to investigate exciting new applications for spark ablation nanoparticles, which resulted in the development of a crude die-attach process using gold nanoparticles. This innovation attracted the attention of Prof. G.Q. Zhang at the microelectronics lab, who sought to use spark ablation technology to develop nanomaterials for microelectronics. Subsequently, I soon started a PhD in his group at the Else Kooi Laboratory (EKL) to investigate several interesting potential applications.
Could you share the specific research topic(s) you explored with the VSPARTICLE tools and why it is significant in your field?
One of the specific research topics I explored with the VSPARTICLE tools was the printing of nanoparticles on silicon wafers and microelectronic devices. To accomplish this, I worked with VSPARTICLE engineers to build a custom setup in the cleanroom. This setup consisted of a custom gas mixing panel, a VSP-G1, and a vacuum chamber with an xyz-orientable nozzle. The flexibility of the VSPARTICLE technology allowed us to print nanoparticles from any bulk metal or metal oxide, enabling us to try a range of materials and explore ideas rapidly.
My research topics varied from investigating nanostructured materials such as thermoelectric materials to printed electronics, printable UV sensors, gas sensors, and functionalizing MEMS devices and chemical sensors. The prototype printer, though more limited than the commercialized printer, offered great customization, enabling the integration of in-situ conductivity measurement setup, mass measurement devices, and even a hot plate.
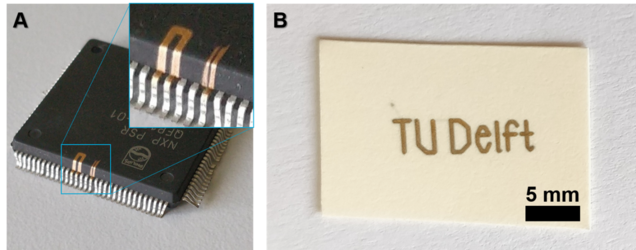
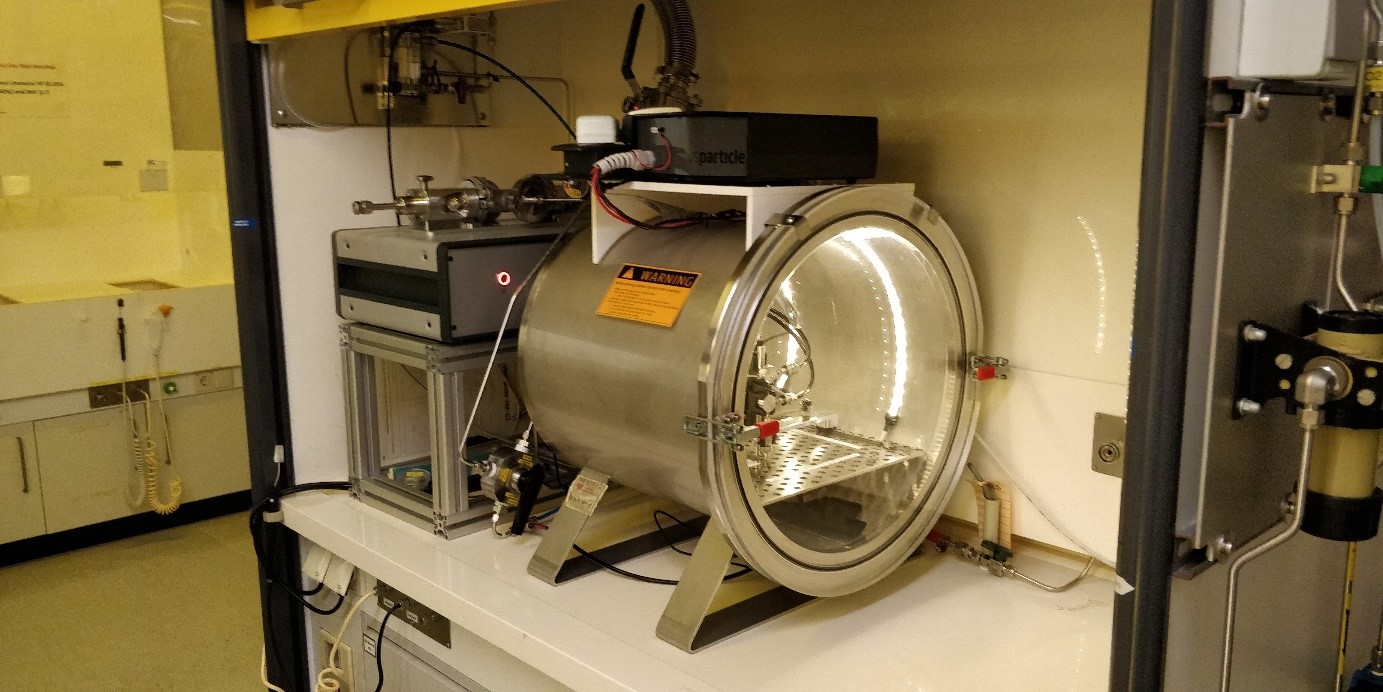
In what ways have the VSPARTICLE tools contributed to the success of your work in comparison to other methods or devices?
The VSPARTICLE tools allowed us to better control the printing process and reproducibility of results. The accurate method I developed to measure the printed mass output using quartz crystal microbalances further enhanced the reliability and consistency of our experiments. They also saved us time and cost by eliminating the need for complex synthesis procedures and inaccurate deposition methods.
Coating a device with nanoparticles typically requires complex synthesis procedures and imprecise deposition methods such as drop casting or lithography. This system addresses this challenge by featuring an accurate printing stage equipped with nozzles capable of reproducibly print sub-mm structures. Over time, as we gained experience with the tool, we achieved more printing accuracy and significantly reduced process development time by leveraging our previous recipes.
In your opinion, what makes the VSPARTICLE tools valuable for other researchers in your field?
The ability to print pure nanostructured films from various metals directly on silicon was a significant advantage of the Nanoprinter. This allowed us to combine the strengths of microfabrication and nanoparticles, integrating special properties of nanoparticles and nanostructured films into semiconductor devices or on-chip applications. We were able to coat chemical sensors, explore printed electronics, and investigate nanostructured materials for thermoelectric applications.
Based on my personal experience, I highly recommend the VSP-G1 and Nanoprinter to colleagues or peers in my field. The key benefits I would like to highlight include simplicity and versatility. The nanoparticle generator is easy to use, has wide material flexibility, and produces a consistent output production rate and particle size. The clean and precise deposition method allows for quick setup of experiments without affecting your microelectronic device. Additionally, the ability to print nanoparticle structures on various substrates within an hour opens up opportunities for rapid material development and exploration of new ideas.
I would like to mention that the equipment we used was a prototype, so it had some limitations in terms of mass output and reliability. However, the newer versions of the VSPARTICLE tools have already shown significant improvements in reliability, speed, accuracy, and ease of use. I believe that the new generations of VSP-P1 Nanoprinters will enable even more advanced devices that utilize printed nanoparticles. Overall, my experience with the VSPARTICLE technology has been extremely positive, and I am confident that they will continue to be a valuable tool for researchers in the field of nanomaterials and microelectronics.
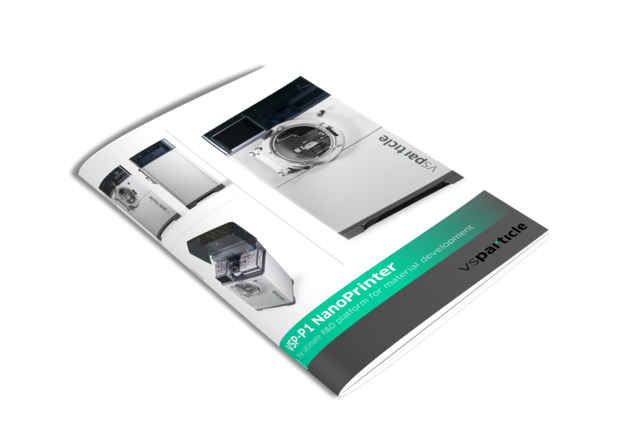
Nanoparticles at push of a button
VSParticle nanoparticle generators and printers enable researchers and material & device manufacturers to synthesize and deposit nanoporous materials in an easy, clean and efficient way.