Spark ablation for nanoporous material production
The discovery of spark ablation for nanoparticle production is a story filled with unexpected brilliance. It all began in the 1970s when a young PhD student, Andreas Schmidt-Ott, was conducting an entirely different experiment. As fate would have it, faulty wiring caused repetitive sparks, and something extraordinary happened—nanoparticles began to form. This happy accident sparked the birth of spark ablation, a technique that has proven far more efficient than anything else available, forever changing the landscape of nanotechnology.
Redefining material properties in the 1980s
Material scientist have always been looking for new methods to change the physical properties of inorganic materials. This process is key in enabling next generation products in many high-tech markets.
Before the 1980s, material scientists relied on basic techniques of mixing different materials to change the physical properties. However, the 1980s marked a turning point with the emergence of quantum size effect in nanotechnology. This phenomenon strongly impacts the physical properties of nanoparticulated inorganic materials as their size decreases to the nanoscale (typically below 10nm). During this transformative period, Andreas Schmidt-Ott started investigating a better method for nanoparticle production. Changing material properties by controlling nanoparticles size introduced a completely new dimension, complementing traditional mixing techniques. In addition, nanoparticulate materials exhibit other unique features that set them apart from conventional materials.
The value of nanoparticles in today’s market
One striking example of how nanoparticles have revolutionized material science is the production of nanoporous materials— substances that are porous on a nanoscale. These materials possess an incredibly large surface area relative to their volume. For instance, just 10g of carbon nanoparticles with a diameter of 5nm can have a surface area equivalent to that of a football field. This significant increase in surface area enhances the reactivity and unique properties of nanoporous materials.
This unique property makes nanoporous materials ideal for applications such as catalysts in hydrogen production from water, where maximizing surface area is key to enhancing catalytic performance. This property is crucial for developing next-generation nanoporous layers, which play a key role in scaling up green hydrogen production, and reducing the reliance on precious metals. For example, achieving tenfold reduction in iridium loading while maintaining high efficiency is needed to not only cut material costs but also support the large-scale adoption of sustainable hydrogen as a future fuel source. This advancement will make hydrogen production more economically viable and environmentally friendly, accelerating the transition to clean energy solutions.
Navigating the hurdles of nanoparticle production with spark ablation
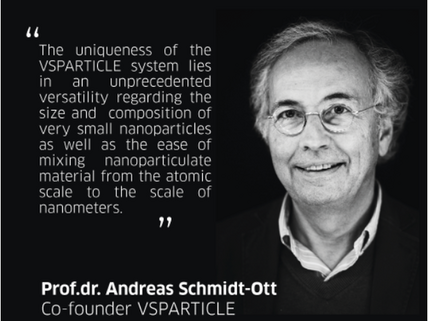
Historically, the production of nanoparticles has primarily relied on wet chemical synthesis, which was well-established before the 1980s. However, when it comes to producing particles smaller than 10 nm, wet chemical methods face several challenges:
- Reproducibility
- Time requirement to develop specific recipes
- Material flexibility
Surface contamination
These bottlenecks partly fuelled the research of Prof. Schmidt Ott into new pathways. After multiple decades of fundamental research, he was convinced that spark ablation was the best synthesis method. In 2013, he and Dr. Tobias Pfeiffer achieved a breakthrough in scaling spark ablation, laying the foundation for bringing this innovative technology to the market.
What is spark ablation?
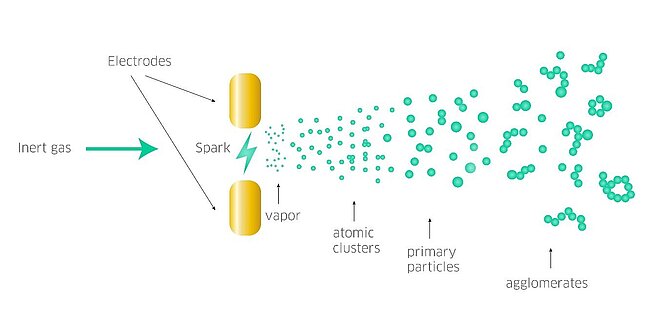
Spark ablation is an innovative method for producing nanoparticles by generating high-energy electrical sparks between two electrodes (metals or semiconductors). These sparks vaporize the electrode material, creating a vapor cloud that quickly cools and condenses into nanoparticles, which remain suspended in the gas as an aerosol. An analogy for this process is boiling water; just as vapor condenses into droplets when cooled, the vaporized material in spark ablation forms fine nanoparticles.
How are nanoparticles assembled into functional nanoporous materials?
To create nanoporous materials, nanoparticles need to be gathered onto a surface, known as a substrate. This step is crucial to immobilize the particles, taking them out of the aerosol and making them part of a usable device. The VSParticle VSP-P1 Nanoprinter is coupled with one or more VSP-G1 Nanoparticle Generator simplifies this process through three sequential automated steps:
- A spark is generated between two electrodes by applying an electric field strong enough to ionize the medium. The plasma formed in the gap reaches a temperature > 20,000°C which ablates rod material from the electrodes into its constituent atoms. Each spark produces a small vapor cloud that mixes rapidly with the inert gas. This gas, at room temperature, accelerates the cooling process, known as quenching, causing atomic clusters to nucleate and condense into primary nanoparticles (2-5 nm).
- The ablated material is carried away from the spark region by the flow of the inert gas. During this transportation stage, the particles may form agglomerates or fractal-like or string-like structures as they collide and stick together.
- The nanoparticles are then deposited onto a substrate from the carrier gas using hypersonic impaction. In this method, the aerosol ((nano)particles dispersed in gas) enters the vacuum chamber through a nozzle with a narrow orifice. The gas flow is accelerated to hypersonic speeds through the nozzle, causing the nanoparticles to follow a focused trajectory and impacting on the substrate surface. Due to the Van der Waals forces and strong metal-metal bonds, the nanoparticles stick to the substrate and to each other, forming a nanoporous thin film. The thickness and pattern of the film can be controlled by adjusting the movement of the substrate on an XYZ-stage, enabling the precise printing of complex nanoparticle patterns without the need for binders.
The VSP-P1 Nanoprinter assembles nanoparticles on the surface, enabling the formation of nanoporous thin films with tuneable properties, including thickness, porosity, patterning and composition/ stoichiometry.
Why is spark ablation leading the next wave of nanotechnology?
At VSPARTICLE, we believe that spark ablation is poised to revolutionize the next decade of nanoporous materials due to several key advantages:
- Powered by electricity: As the role of renewable energy sources continues to take over electricity generation, this technology is driven by electrical power. This makes it well-aligned with the growing trend toward cleaner and more affordable energy solutions.
- Smallest stable nanoparticles: The technique enables the production of the smallest stable nanoparticles, which are crucial for fabricating advanced thin-film nanoporous layers. This high level of precision places Spark ablation ahead of other technologies, allowing for the development of cutting-edge materials with superior properties.
- Clean surfaces for electrochemistry: Electrochemical processes require well-controlled and uncontaminated surfaces for optimal performance. Unlike traditional chemical synthesis methods that leave residual pollutants on nanoparticle surfaces, this technology uses a chemical-free approach, resulting in purer and more effective materials.
- Direct printing of nanoporous layers: Spark ablation enables the direct deposition of nanoparticles onto various surfaces. This method eliminates the need to convert nanoparticles into powders or use binders, which are common in current industrial practices and can compromise the properties of the nanoparticles. Typically, nanoparticles are processed into a powder before being adhered to substrates, such as copper foil for batteries. However, in powders, nanoparticles cluster to larger units which cannot be separated. Furthermore, chemicals or adhesives are required for surface adhesion. Consequently, the most effective way to print nanoporous layers without chemicals is to directly deposit the small nanoparticles themselves.
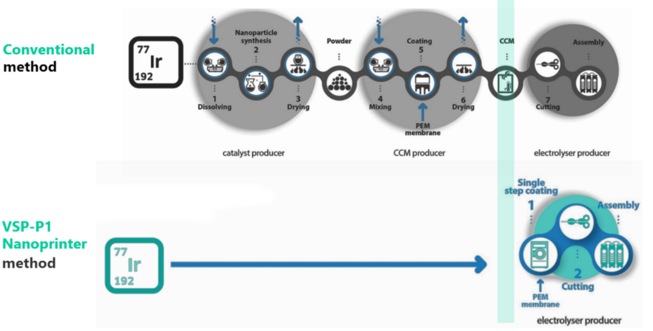
- Material agnostic: The technology is versatile enough to process two-thirds of the periodic table with minimal modifications. Unlike chemistry-based methods, which require distinct recipes for each material, spark ablation's material-agnostic approach is vital for a wide range of applications, including Self Driving Labs (SDL). We can utilize the same device with minimal modifications to advance two-thirds of the periodic table. In contrast, chemistry-based synthesis demands the creation of entirely new recipes for each nanoparticle. This material-agnostic approach is key in enabling the right material synthesis platform for Self- Driving Labs (SDLs).
- Configurable hardware: The modular design of the system offers maximum flexibility for different industrial processes and customer requirements. This adaptability ensures that the spark ablation technology can be tailored to meet various demands in material synthesis and manufacturing.
- In-line process control: The technology supports real-time quality control through established methods for measuring nanoparticle size and concentration. This capability provides a significant advantage in maintaining precise and consistent production outcomes.
With these unique benefits, spark ablation is setting a new standard in nanotechnology, driving the development of next-generation nanoporous materials for a variety of advanced applications.
Expanding the horizons of combinatorial material discovery
This method dramatically enhances the potential for combinatorial material discovery by enabling researchers to investigate countless combinations of approximately 70 elements from the periodic table. This leads to an immense array of novel materials, each with distinct properties. Scientists can generate large datasets with this automated system that can train AI models to identify optimal materials. Notably, mixed catalysts have been shown to outperform their individual components.
Imagine an automated system producing groundbreaking catalysts every minute, with AI and quantum computing predictions speeding up the search for the best catalyst. The ultimate aim is to replace rare, expensive catalyst materials with more abundant alternatives. Once a promising material is identified, it can be scaled up for industrial production using the same technique. This will indeed, transform fields like catalysis and beyond by facilitating the rapid discovery of innovative materials with enhanced functionalities.
Acknowledgment
Special thanks to Prof. Andreas Schmidt-Ott (co-Founder), Aaike van Vugt (CEO) and Nayab Azam (Technical Content Writer) for contributing and sharing their knowledge and expertise in writing this blog post.
Comments
No Comments