Advancing CO₂ electrolysis with VSParticle technology
CO₂ electrolysis has emerged as a mechanism which converts CO₂ into valuable products. This technology not only offers a way to mitigate GHG emissions but also presents an opportunity to establish a circular carbon economy, avoiding further extraction of fossil fuels from underground and integrating carbon flows for the production of essential fuels and chemicals.
CO₂ electrolysis has seen slow progress over the past few decades, despite its potential to transform carbon emissions into valuable fuels and chemicals. The primary challenge has been the development of efficient and durable catalyst capable of operating at a commercial scale. While research has advanced, no commercial catalyst has yet made it to the market, leaving this promising technology underdeveloped. To exploit the full potential of CO₂ electrolysis, a massive acceleration in innovation and scaling is urgently needed. Through scaling this solution, we are able to convert a problem, i.e., CO₂ that causes global warming to a solution in the form of sustainable fuels, chemicals and materials.
In this blog we explore CO₂ electrolysis to gain a deeper understanding of its potential in developing a sustainable future. We look at the fundamental principles of CO₂ electrolysis, its products, major road blocks towards its progress and the solution that VSParticle offers to accelerate the development of CO₂ electrolysis.
What is CO₂ Electrolysis?
CO₂ electrolysis is an electrochemical process that reduces CO₂ into various C1, C2 and C3 type products, depending on factors such as the components (i.e. cell type, electrodes, catalyst etc.) and reaction conditions (i.e. voltage, temperature, and pressure). The process takes place in an electrolyzer, similar to those used for hydrolysis (a.k.a. water electrolysis). The system consists of these key components:
Cathode: Negatively charged electrode where CO₂ is reduced to products such as formate, carbon monoxide, methane, along with ethylene and ethanol at a high reaction rate. CO₂ is fed in the gas phase to the cathode; and the products can be a mixture of gas, liquid and pervaporates.
Anode: Positively charged electrode where the Oxygen Evolution Reaction (OER) occurs. A saline water is fed through a liquid pump; and the products are oxygen gas and hydrogen ion (or hydroxide depending on the reaction pH).
Electrolytes: A saline water which conducts ions between the electrodes, facilitating the reaction.
Membrane: A polymeric thin sheet (thick as a piece of hair) which separates the cathode and anode, allowing selective ion transport while preventing gas crossover.
Voltage source: Electrical power unit which provides sufficient potential (E) to generate a current to transfer electrons from anode to cathode.
Below is a sketch of the core of the electrolyser This setup enables the conversion of CO₂ into valuable chemicals and fuels.
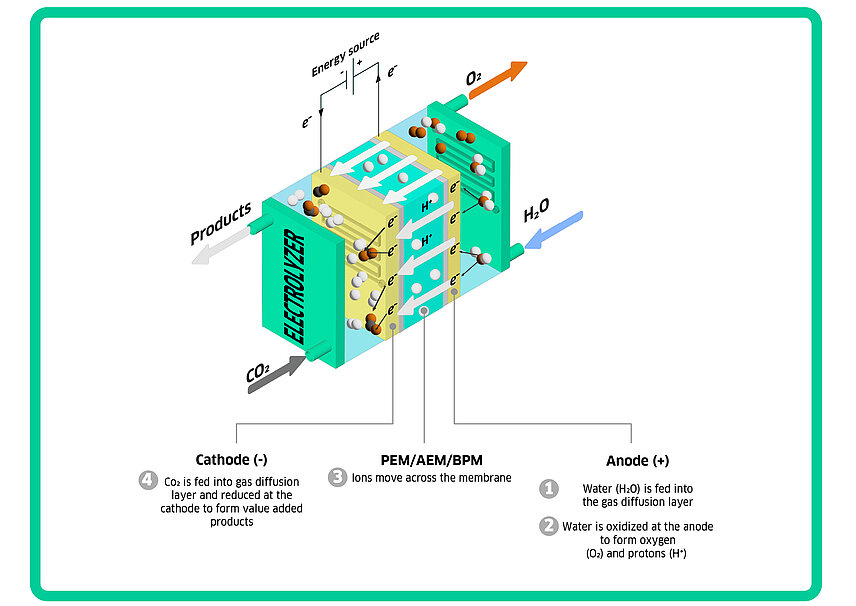
Why is CO₂ electrolysis essential in solving climate change?
CO₂ conversion plays a key role in addressing climate change since merely halting emissions isn't enough to stay within the 1.5°C temperature increase target. CO₂ volumes that are residing in the atmosphere continue to cause global warming effects. This is why we need to not only stop additional CO₂ from getting into the atmosphere but also remove CO₂ levels that are above acceptable limits. Direct Air Capture (DAC) is one such technology that is being developed to capture and remove CO₂ from the atmosphere. Taking CO₂ out from the atmosphere is critical to getting a chance to remain below 1.5°C limit. The Earth’s temperature has already increased by 1.1°C above pre-industrial temperature levels. CO₂ electrolysis can use that CO₂ to make sustainable fuels, chemicals and materials. It is important to mention that capturing CO₂ from atmosphere is very expensive right now. However, CO₂ capture technologies from techno-sphere (e.g., energy industry) and biosphere (e.g., biomass used for bioenergy production) are relatively more mature and provide low hanging fruit for climate mitigation in the short and medium term.
Because of increased global warming, oil and gas companies, power producers as well as heavy industry are faced with a massive challenge to decarbonize. The EU legislation now requires companies to report on their climate performance in terms of their annual carbon footprint, followed by a science based 2030 climate mitigation target for their own operations as well as value chain. This would require companies to set not just scope1(e.g., process energy) and scope 2 (e.g., electricity use) emission reduction targets but also scope 3 (e.g., combustion emissions from products & fuels).
To reduce scope 3 emissions, oil & gas companies are looking for sustainable alternatives such as renewable diesel, Sustainable Aviation Fuel (SAF), bio-methanol as well as biomethane. In the EU, there is a mandatory obligation on gasoline and diesel suppliers to blend sustainable fuels in their supply as part of the effort to reduce at least 55% GHG emissions by 2030 compared to 1990 levels. The obligation has been extended to jet fuel suppliers recently which would require massive upscaling of SAF in the coming years to decarbonize aviation. These regulatory measures require oil & gas companies to reduce their scope 3 emissions next to scope 1 & 2 emissions.
Furthermore, while renewable electricity generation peaks at midday, energy consumption rises in the afternoon, creating a mismatch between supply and demand that batteries alone cannot resolve. This is why synthetic fuels that are produced through (surplus) renewable electricity and /captured CO₂ conversion, could be the key to provide energy system balancing reducing costs at the system level.
CO₂ electrolysis in an integrated closed loop carbon cycle
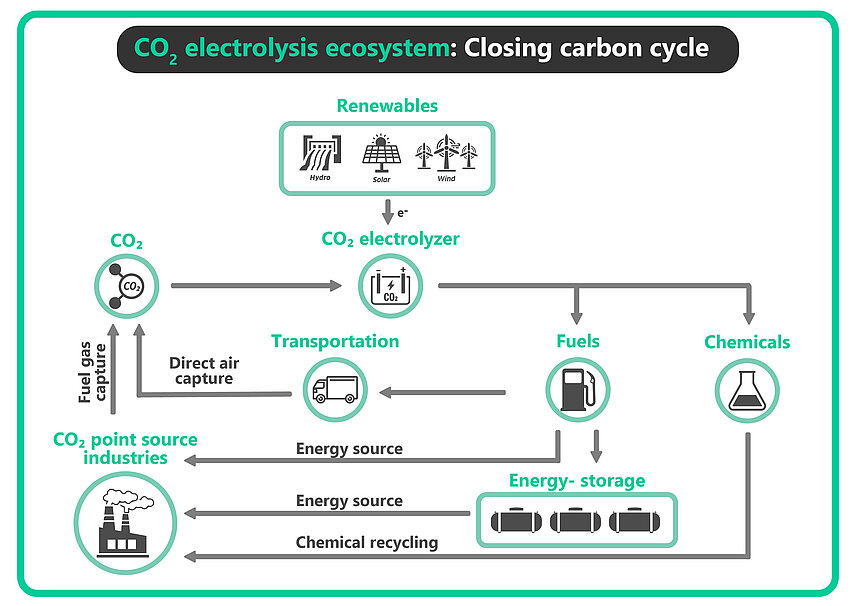
In CO₂ electrolysis, one of the main products of CO₂ reduction reaction (CO₂RR) is carbon monoxide (CO), which is often combined with H₂ to make syngas (CO + H₂). CO is a key building block to produce fuels such as methanol, ethanol and synthetic gasoline running the transportation sector. The integration of CO₂ electrolysis avoids the environmental impact of fossil fuels, thereby offering a sustainable alternative. These fuels when combusted would still emit CO₂ which can be captured and fed back into the production system to close the loop.
CO₂RR can also produce a wide variety of sustainable chemicals and materials like ethylene, ethanol and formic acid. Ethylene is used in the chemical industry to make polyethylene and other polymers while formic acid is commonly used in the agricultural, pharmaceutical, and textile industries. Formic acid can also be used directly in fuel cells for energy storage and is a useful hydrogen carrier. Capturing CO₂ and its electrochemical conversion to hydrocarbons offer a potential pathway for carbon-neutral chemical alternatives.
However, requirement of high energy input, due to the high stability of CO₂ molecule at normal temperature and pressure, low selectivity for desired products and high cost of current catalyst materials make it a challenge to scale up the technology.
Current state-of-the-art technologies and key roadblocks
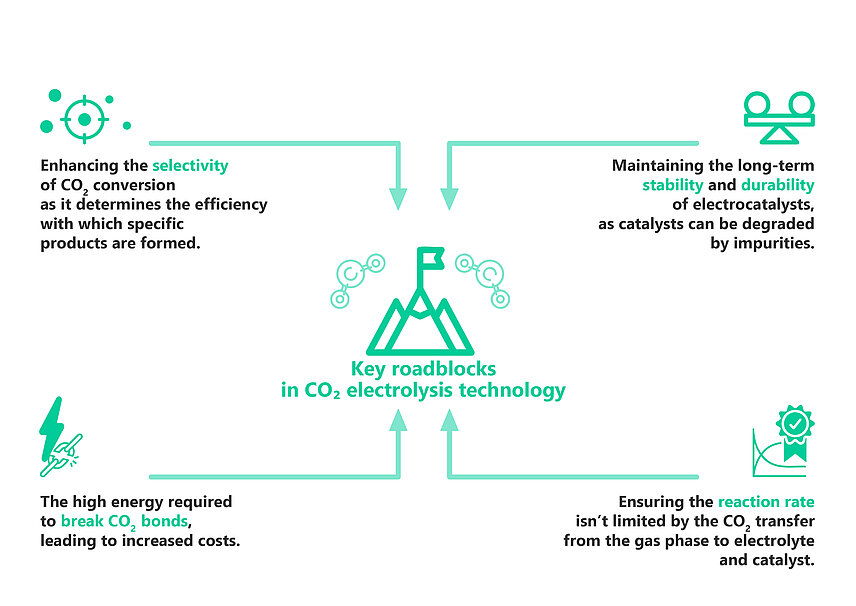
Despite recent progress in component design at pilot-scale, CO₂ electrolysis remains a fringe technology. Its relatively high capital and operating costs are hindrance for its practical applications and market penetration. However, this is contingent on a variety of factors such as electricity pricing and markets, policy as well as the performance of electrolyzer components. Table below provides an overview of different noteworthy initiatives aimed at advancing CO₂ electrolysis technology.
Technology (location) | Scale | Catalysts | Target Products |
---|---|---|---|
Twelve (Berkeley, USA) | Lab-scale | Anode: IrO₂, cathode: Ag Nanoparticles supported on carbon foam | CO and O₂ |
Dioxide materials (Boca Raton, USA) | Lab-scale | Anode: IrO₂ or RuO₂, cathode: carbon paper coated with silver/ionomer mixture | >95% selectivity to CO |
Carbon electrocatalytic recycling Toronto (CERT) (Toronto, Canada) | Lab-scale/pilot-scale cell | Anode: made from cheap and conventional abundant earth metals, cathode: nanostructured metals based on copper | 70% selectivity for C₂H4 |
Siemens and Evonik (Germany) | Lab-scale | Anode: IrO₂ coated titanium, cathode: silver gas diffusion electrode based on oxygen depolarization cathode (ODC used in industrial chlorine–alkaline electrolysis) | 70% selectivity for CO, then CO fermentation to higher alcohols |
TNO (Netherlands) | Pilot-scale | Not disclosed publicly | CO and Formic acid |
Kanan Lab (Stanford) | Lab-scale | Not disclosed publicly | |
Dioxycle (France) | Pilot-scale | Not disclosed publicly | Ethylene |
eChemicals (Hungary) | Lab-scale | Not disclosed publicly | CO |
Aircompany (USA) | Pilot-scale | Not disclosed publicly | Ethanol, methanol, water and paraffins |
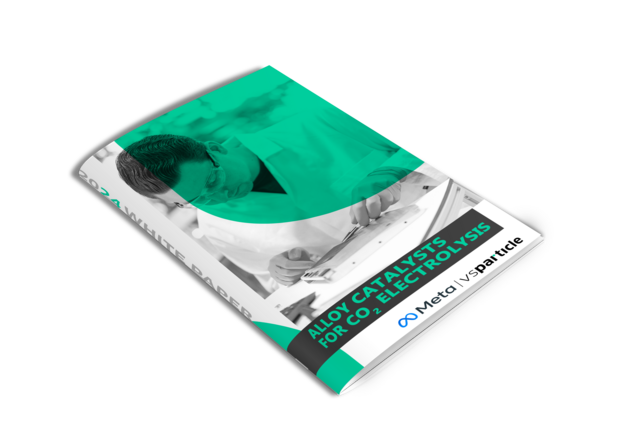
Get access to detailed analysis of alloy catalysts datasets synthesized with VSParticle technology for Meta's Open Catalyst Experiments 2024
Engineering the electrocatalyst coated on Gas Diffusion Layer (GDL)
One key area of innovation is the engineering around the electrocatalysts. Through innovation in this space, many of the aforementioned inter-linked technical challenges have been addressed. [3] The cathode in a CO₂ electrolyzer needs to provide active catalyst sites to facilitate sufficient contact for CO₂, electrolyte and catalysts to transfer electrons and ions (Figure 3). [4]
For industrial scale CO₂ processes, achieving high current density (CD) over 1 A/cm2 is essential because it directly relates to the rate of CO₂ conversion into desired products. Therefore, 3D-structured electron conducting substrates coated with catalysts are preferred compared to planar electrodes. Gas diffusion electrode (GDE); consisting of a gas diffusion layer (GDL), catalyst layer (CL) and current collector, has emerged as a key area of interest, offering advantages in improving mass transfer rates and reaction efficiencies. Studies have shown that optimizing GDE designs can lead to higher current densities (600 mA/cm2) and Faradaic efficiencies (close to 100%). [5]
Additionally, the catalyst material, its composition, surface orientation, morphology, and size are critical factors that directly influence the reaction kinetics. They play a key role in determining the surface reaction rate and selectivity in CO₂ reduction. Therefore, by carefully tuning the composition and structure of catalysts, researchers are unlocking new possibilities for efficient CO₂ reduction, making this area of study particularly relevant.
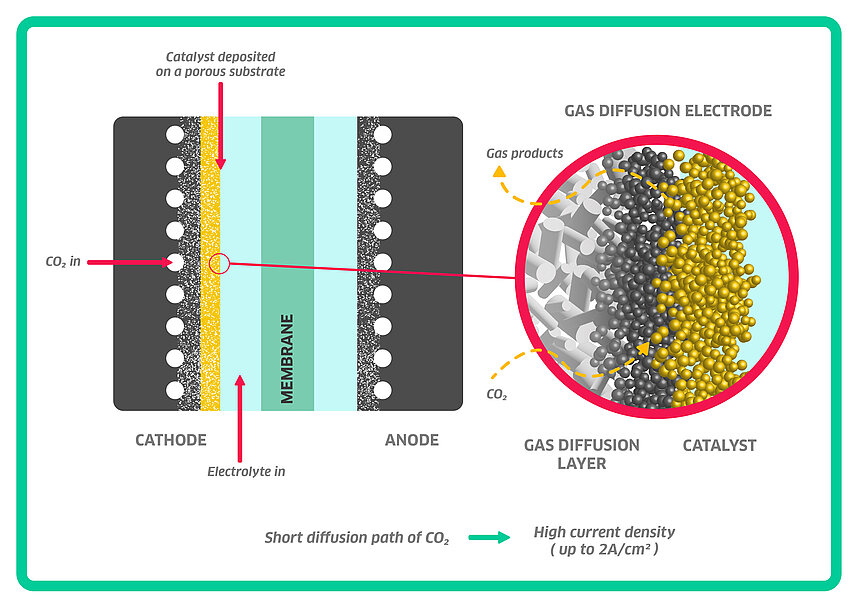
Key challenges in achieving high-quality nanoporous catalyst layers
When researchers attempt to fabricate nanoporous catalyst layers, they often face immense challenges that lead to slow progress. The process is far from simple. In the lab, creating these delicate structures demands extreme precision, time, and effort. The pain lies in the fact that traditional methods, like wet coating, are not only labor-intensive but also unpredictable. In this method, a liquid solution containing catalysts is deposited on a substrate and allowed to dry. However, this drying process can lead to uneven distribution of the nanoparticles, blockages, and loss of the porous structure, which is essential for maximizing the catalytic efficiency.
Additionally, controlling the porosity and thickness across larger areas is highly challenging, resulting in suboptimal performance and poor reproducibility. It’s a tedious, trial-and-error process that can take months of painstaking work, often leading to inconsistent results or failure. This frustration and the inability to streamline the creation of uniform catalyst layers hinder significant advancements.
Unlocking the potential of CO₂ conversion with VSParticle technology
VSParticle technology revolutionizes catalyst manufacturing by replacing the traditional wet coating method with a precise vapor deposition process using the VSP-P1 Nanoprinter. This approach allows for highly controlled, uniform nanoporous layer formation, significantly reducing time, labor, and uncertainty. By streamlining the process, it transforms what used to take months into a scalable, efficient workflow, accelerating the development of consistent, high-performing catalysts. This breakthrough not only enhances quality but also expands the possibilities for innovation in energy conversion, storage, and other advanced applications.
VSParticle's VSP-P1 Nanoprinter is making significant strides in CO₂ electrolysis research by enabling the precise synthesis of electrocatalysts with varying sizes, compositions, and morphologies. Their groundbreaking work highlights the potential to enhance both the reaction rate and Faradaic efficiency (selectivity) of catalysts towards desired products.
A key achievement from VSParticle is the successful deposition of electrocatalyst on silicon wafers, GDL and membranes. Through extensive optimization, it was ensured that the catalyst is not oxidized to guarantee longevity, thus enabling cost reduction. The most promising materials were synthesized and produced on flat substrates and identified through X-Ray Diffraction (XRD) validating their metallic state and precise composition. Later on, these were reproduced on GDLs and rigorously tested in electrolyzer cells under industrially relevant conditions.
While the future of CO₂ electrolysis is promising, ongoing research and development are essential to overcoming current challenges. The collaboration between academia and industry will be vital in advancing this technology and bringing it to market. With continuous innovation in materials, catalysts, and reactor designs, CO₂ electrolysis has the potential to play a pivotal role in achieving a sustainable, low-carbon future.
Acknowledgment
Special thanks to Nayab Azam (Technical Content Writer) and Erdem Irtem (Application Specialist) for contributing and sharing their knowledge and expertise in writing this blog post.
References
Garg, S., Li, M., Weber, A. Z., Ge, L., Li, L., Rudolph, V., Wang, G., & Rufford, T. E. (2020). Advances and challenges in electrochemical CO2 reduction processes: an engineering and design perspective looking beyond new catalyst materials. Journal of Materials Chemistry A, 8(4), 1511–1544. doi.org/10.1039/C9TA13298H
Nguyen, T. N., & Dinh, C.-T. (2020). Gas diffusion electrode design for electrochemical carbon dioxide reduction. Chemical Society Reviews, 49(21), 7488–7504. doi.org/10.1039/D0CS00230E
Ramdin, M., Moultos, O. A., van den Broeke, L. J. P., Gonugunta, P., Taheri, P., & Vlugt, T. J. H. (2023). Carbonation in Low-Temperature CO2 Electrolyzers: Causes, Consequences, and Solutions. Industrial & Engineering Chemistry Research, 62(18), 6843–6864. doi.org/10.1021/acs.iecr.3c00118
Samu, A. A., Szenti, I., Kukovecz, Á., Endrődi, B., & Janáky, C. (2023). Systematic screening of gas diffusion layers for high performance CO2 electrolysis. Communications Chemistry, 6(1), 41. doi.org/10.1038/s42004-023-00836-2
Wakerley, D., Lamaison, S., Wicks, J., Clemens, A., Feaster, J., Corral, D., Jaffer, S. A., Sarkar, A., Fontecave, M., Duoss, E. B., Baker, S., Sargent, E. H., Jaramillo, T. F., & Hahn, C. (2022). Gas diffusion electrodes, reactor designs and key metrics of low-temperature CO2 electrolysers. Nature Energy, 7(2), 130–143. https://doi.org/10.1038/s41560-021-00973-9
Comments
No Comments