Sparking a revolution in catalysis by mixing anything with anything
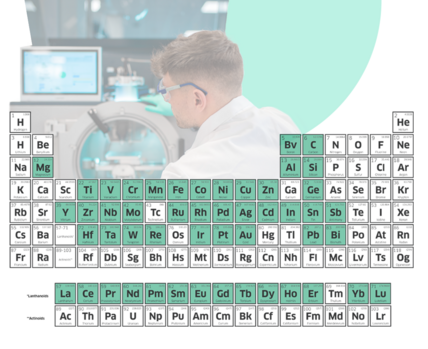
By Prof. Andreas Schmidt-Ott
Spark ablation in gasses, first introduced in 1988 [1], has intensively been used by research institutions and more recently “discovered” by industry as a technology of unprecedented flexibility in producing nano-products based on particles in the size range from clusters of a few atoms to nanoparticles some tens of nanometers in diameter. Such particles are, among others, the building blocks of catalysts. Using a catalyst means saving energy. Improving a catalyst means saving more energy, which is a key goal in overcoming the energy crisis.
State of the Art Regarding Catalyst Materials in General
The answers given by the artificial intelligence chatbot ChatGPT should usually be confirmed by further research. They correspond to something like the present general belief of experts in the relevant field. Just for fun, I asked ChatGPT to give me a list of commonly used metal catalysts. The chatbot came up with the following list:
Pt, Pd, Ru, Ni, Fe, Mo, V, Cu, Ag, Zn.
Application examples were given for each one of them. It is striking that all these catalysts involve only a single element! My second question to the chatbot was thus:
“Are such pure catalysts better than catalysts involving two or more metals?”
The most important parts of the answer were:
“A bimetallic or multimetallic catalyst may be more effective because the combination of different metals can provide synergistic effects, such as increased selectivity or activity.”
Furthermore,
“In general, bimetallic and multimetallic catalysts are becoming more popular in industry because they often exhibit enhanced catalytic activity and selectivity compared to single-metal catalysts.”
These answers already imply that an enormous potential is attributed to producing mixed nanoparticles in the size range typically used for catalysts. An aspect the chatbot did not consider but that should certainly be added is the following: The number of catalytic materials available is virtually unlimited if catalysts based on nanoparticles of any mixture are easily prepared.
These thoughts triggered my third question to ChatGPT:
Regarding pure metal catalysts, there is a very limited number N of possible choices of elements, smaller than 100. However, there is a virtually unlimited number M of possible choices of mixed catalysts, even if only very stable ones are considered. So, the ratio M/N is such a high number that it is amazing that pure catalysts still play a significant role with regard to mixed ones. What are the likely reasons for this?
The answer includes the following likely reasons:
“The technology for pure catalysts is established, and the corresponding intellectual property may be protected by patents. switching to a different type of catalyst would require significant investment and effort …”
and
“There are challenges of synthesizing mixed metal catalysts, and they may be of higher cost.”
In other words, Despite the enormous potential of alloyed or doped catalysts, they represent a disruptive technology. Conventional processes for catalyst production are strong for pure catalysts, and a convincing new approach of producing mixed nanostructures is required.
The potential of spark mixing
The technology waiting to be used can be called “Spark Mixing,” and it was evidently not known to ChatGPT. What is spark mixing?
It is based on spark ablation, meanwhile a well-established technology for the production of nanoparticles and atomic clusters [1, 2, 3]. In a nutshell, repetitive spark discharges of suitable energy are produced between two electrodes, as illustrated in Fig. 1. Each discharge evaporates a small amount of material from the electrodes, and the vapor condenses within the carrier gas to form nanoparticles. In the resulting aerosol, these are grown to the desired size and carried to the place where they are needed to assemble the product. Catalysts produced this way have already been shown to have properties that are superior to conventional ones (see [12, 13, 14])
The power of producing mixed nanomaterials by spark ablation [3, 4, 5, 6, 7] is less known. This process is referred to as spark mixing, and, in particular, three possibilities of carrying it out have been demonstrated:
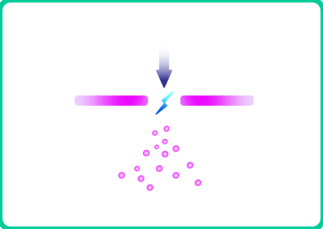
1. The electrodes already consist of an alloy. A remarkable feature of spark ablation is that at suitable spark durations and spark energies, the nanoparticles produced have the same composition (mixing ratio) as the electrodes.
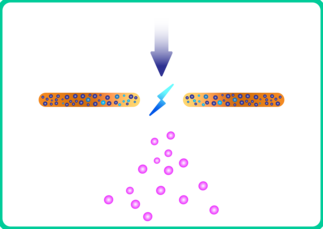
2. Many metal combinations are immiscible but form alloys within nanoparticles smaller than 10 nm [5]. This enormously expands the space of possibilities of producing catalytic particles that have never been produced before. Electrodes consisting of compressed mixed powders have been used in such cases [8].
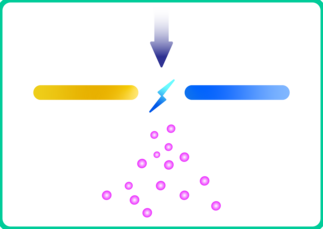
3. Alloyed nanoparticles have also been produced by applying oscillatory sparks between electrodes of different materials [9]. The mixing ratio is tuneable by the electrical characteristics of the discharge as well as the diameters of the electrodes.
.
So spark mixing leads to alloyed nanoparticles. By adjusting the electrical characteristics as well as the relative electrode diameters [10] and/or the composition of the electrodes, an unlimited variety of mixing ratios can be obtained.
Apart from the 7 noble metal elements (Gold, platinum, ruthenium, rhodium, palladium, osmium and iridium), catalysts based on non-noble metals (mainly their oxides) are of interest. Oxidation of the nanoparticles in the gas stream to form the oxide of choice or other compounds is easily accomplished [2, 11].
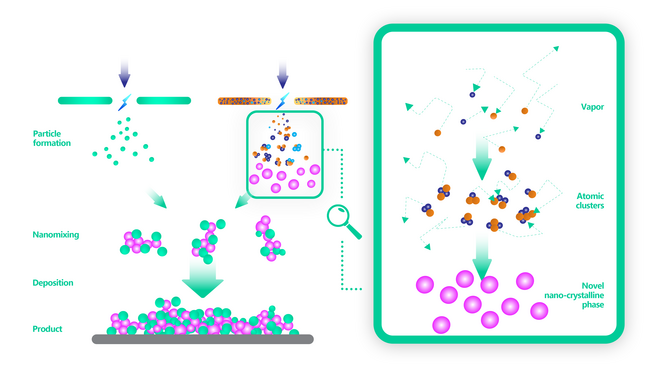
Apart from spark mixing for forming alloyed nanoparticles, the co-existence of different materials in nanometer proximity is often desired in connection with co-catalysts or catalyst-substrate interactions. Using spark ablation, such nano-scale mixtures can easily be produced by mixing the aerosols from different spark generators. The particles in the mixture are deposited onto a substrate, as illustrated in Fig. 4, where they form a nanoporous layer with an extremely high surface area, as required for a catalyst.
As the figure suggests, one or both nanoparticle materials may consist of an alloy produced by spark mixing. One of the components may, for example, be a typical substrate material, such as titanium dioxide, in the form of larger particles.
Conclusions and future perspectives
The examples above reveal an unlimited potential of spark ablation for producing improved catalysts. However, from the myriad of possibilities concerning material size and structure, combinations have to be found that represent improvements in catalytic behaviour with respect to the state of the art. Here, the great flexibility of the method comes into play. In contrast to conventional, wet chemical methods of catalyst production, the same production process (spark ablation plus printing) can be used for any new combination of materials. In the search for better catalysts, one will start making test samples based on theoretical predictions or educated guesses or simply start out from the pure metal presently applied and mix in other components, either to form alloys or complex heterogeneous nanostructures. If the resulting catalysts behave worse than the state of the art, forget about them, and if they perform better, we are a step further but can continue the search to improve again. Impressive examples have been reported, where the mixed catalyst performs better than the components it is composed of [12, 13]. The second example demonstrates a successful combinatorial search for such superior mixed materials. The first example is based on spark ablation, and the product already has a high surface area as required for a catalyst.
An automized system, producing a catalyst that has never been produced before every minute, could be implemented. Artificial intelligence and, ultimately, the predictions of a quantum computer will accelerate the search in the future. The ultimate goal is to replace catalysts using rare, expensive materials by mixtures of abundant materials.
Gas phase processes for nanoparticle production can reach much higher levels of purity than conventional liquid-based ones. This leads to products that are better defined in their chemical nanostructure, and it is to be expected that theoretical predictions have a higher success rate. Chemical engineers have to account for the fact by experience that the end product will never have the ideal chemical nanostructure but that deviations that depend on the production process are unavoidable. Spark ablation offers another great advantage here: The process used in the screening experiment can be transferred to the scale of an industrial process. For discovery, one spark gap is sufficient. For production, it can be numbered up to any production rate, keeping the history of every particle from its formation to its deposition onto the substrate very similar.
Industrial implementation
The leading company developing this technology is VSParticle in Delft, The Netherlands. The impressive growth of this company is based on increasing demand from research and industry for flexible nanoparticle production and 3D-printing of nanoparticles onto virtually any surface to form nanoporous structures. Catalysis is an obvious sector driving this demand, and chemical sensors is another. VSParticle concentrates on the world's big challenges, like climate change, the energy crisis, and material scarcity. These problems urgently need solutions, and VSParticle's technology has combined spark ablation with a novel 3D printer to accelerate these solutions. Enhancing the efficiency of green hydrogen production to replace fossil fuels is one of the main goals.
References
[1] S. Schwyn, E. Garwin and A. Schmidt-Ott, Journal of Aerosol Science, 1988, 19, 639–642.
[2] A. Schmidt-Ott, Ed., Spark ablation: building blocks for nanotechnology, Jenny Stanford Publishing, Singapore, 2020.
[3] Feng, J., Biskos, G. & Schmidt-Ott, A. Toward Industrial scale synthesis of ultrapure singlet nanoparticles with controllable sizes in a continuous gas-phase process. Sci. Rep. 5, 15788 (2015).
[4] N. S. Tabrizi, Q. Xu, N. M. van der Pers, U. Lafont and A. Schmidt-Ott, J Nanopart Res, 2009, 11, 1209–1218.
[5] N. S. Tabrizi, Q. Xu, N. M. van der Pers and A. Schmidt-Ott, J Nanopart Res, 2010, 12, 247–259.
[6] Pfeiffer, T. V., Feng, J. & Schmidt-Ott, A. New developments in spark production of nanoparticles. Adv. Powder Technol. 25, 56–70 (2014).
[7] Franzén, SM Jönsson, L, Ternero, P, Kåredal, M, Eriksson, AC, Blomberg, S, Hübner, JM, Messing, ME, Compositional tuning of gas-phase synthesized Pd-Cu nanoparticles, to be published in Nanoscale Advances
[8] Lafont, U, Simonin, L., Tabrizi, N.S., Schmidt-Ott, A., Kelder, E.M., Synthesis of Nanoparticles of Cu, Sb, Sn, SnSb and Cu2Sb by Densification and Atomization Process, Nanoscience and Nanotechnology 9, 2546, 2009.
[9] Feng, J.,Ramlawi, N.,Biskos, G., Schmidt-Ott, A. (2018), Internally mixed nanoparticles from oscillatory spark ablation between electrodes of different materials, Aerosol Science and Technology, 52:5, 505-514
[10] Petallidou, K.C., Ternero, P., Messing, M.E., Schmidt-Ott, A., Biskos, G., Tuning atomic-scale mixing of nanoparticles produced by atmospheric-pressure spark ablation, to be published in Nanoscale.
[11] Isaac, N. A., Valenti, M., Schmidt-Ott, A. & Biskos, G. Characterization of Tungsten Oxide Thin Films Produced by Spark Ablation for NO2 Gas Sensing. ACS Appl. Mater. Interfaces 8, 3933–3939 (2016).
[12] J. Feng, D. Chen, P.V. Pikhitsa, Y. Jung, J. Yang, M. Choi, Unconventional Alloys Confined in Nanoparticles: Building Blocks for New Matter, Matter 3, 1646–1663 (2020).
[13] Brian Rohr, Helge S. Stein, Dan Guevarra, Yu Wang, Joel A. Haber, Muratahan Aykol, Santosh K. Suram and John M. Gregoire, Benchmarking the acceleration of materials discovery by sequential learning, Chem. Sci., 2020, 11, 2696.
[14] Sarka Drdova, Min Gao, Olga Samblov, Robin Pauer, Zhouping Zhou, Sofia Dimitriadou, Andreas Schmidt-Ott and Jing Wang, Precursor- and waste-free synthesis of spark-ablated nanoparticles with enhanced photocatalytic activity and stability, towards airborne organic pollutant degradation, to be published in Environmental Science: Nano
Comments
No Comments