How and why to make nanoparticles?
Nanotech pioneer, Andreas Schmidt-Ott, discusses the evolution and the production of building blocks for nanotechnology from the gas phase.
How did you invent the Spark Ablation technique?
By accident! When I was a PhD student in the 1970s, my supervisor told me to make tiny particles, but he didn’t tell me how. We were only interested in the basic properties of these particles, so he asked me to do it somehow, “the method is not important”. At that time, a method of making small particles by exploding wires was known. The term “nanoparticle” was not yet used. They were called “small particles” or “clusters” (coming from atomic clusters). Properties of nanoparticles were not well known yet. There were theoretical predictions about such particles behaving basically different from large pieces of material, but there was practically no experimental evidence.
I first tried exploding wires, and it worked out somehow, but it was not practical because it didn’t allow you to have a continuous output for an experiment. If you want to study particles' basic properties, you need a continuous source.
To study the particle properties, depositing them onto a surface was not desirable because that would change their properties. The particles have to be suspended in a medium that does not interact with them, like a noble gas. In a vacuum they would fall down like stones, so you would have them only for a very short time. So I took a big capacitor, which instantaneously releases electrical energy into a wire. The wire explodes and turns into small particles that float in the surrounding noble gas.
One day there was a bad contact in the set-up, the wires were not properly connected, and when I applied the high voltage, there were sparks at the bad contact. There was a nanoparticle detector attached to the machine, which detected particles! I was surprised, because when the wire did not explode, repetitive sparks accidentally became a continuous source of nanoparticles.<o:p></o:p>
I became curious about this result and built a small device to reproduce the sparking process. The machine was nothing more than a glass tube with two electrodes at a fixed distance and a power supply to induce spark formation between them (see Fig. 2).
Fig. 3 shows a rebuilt model of the first spark ablation nanoparticle generator.
From the beginning of my tests, I noticed unique benefits of using spark ablation that I couldn’t find in other techniques. For instance, with exploding wires, you obtain particles with a very wide size distribution ranging from nanoparticles to microparticles, the latter being a thousand times larger than the former, while spark ablation produces particles that are not too different in size, and this size is variable.
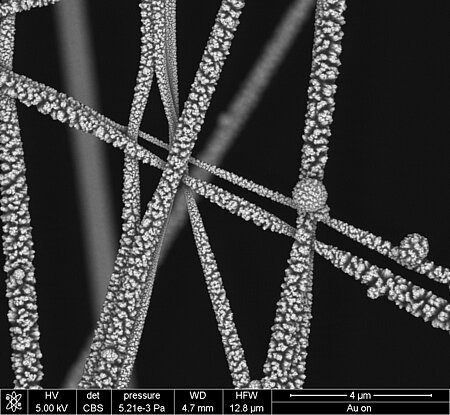
What was the connection between the research and starting the company?
As a researcher, you have a lot of good ideas, but with most of them, you can’t make any profit. Indeed, from the invention of gas phase spark ablation for nanoparticle production, it took many decades until founding a company appeared promising. The demand for nanoparticulate products has to be high enough, and when we founded the company, we clearly saw that there was a strongly rising trend in that direction, which is now accelerating substantially.
That happened in 2014, when Aaike van Vugt (now CEO of VSPARTICLE) and I sat together in connection with his master thesis, in which he had produced very high surface area nanostructures (see fig. 1) by using small fibers (with diameters in the higher nanometer range) and passing nanoparticles around 5 nanometers in diameter suspended in argon through a web of such fibers. The particles then adhere to the fibers and form a nanoporous layer. We thought about commercializing this way of producing nanostructured material. The field of nanotechnology was growing, and there was an increasing need for particle-based materials, such as catalysts, batteries, and sensors.
Tobias Pfeiffer (now CTO of VSPARTICLE), who had already achieved substantial improvements in the spark process in the frame of his Ph.D. thesis, joined the team, and the three of us founded VSParticle.
Today, nanotechnology is everywhere, and nanoparticles can be seen as building blocks of future technology.
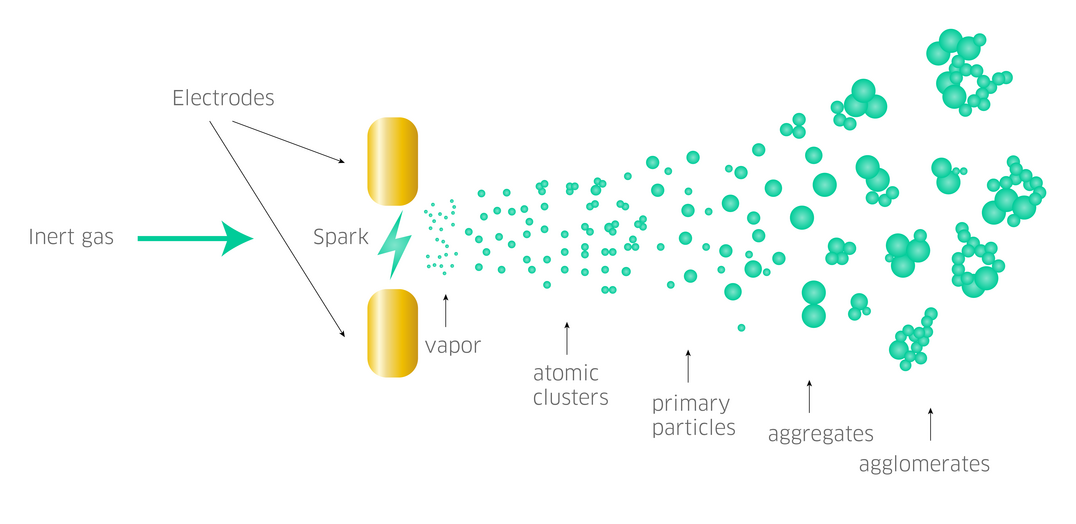
What did you want to enable people to do?
We had the feeling that the timing was right and that we should be the first ones to enable the generation of nanomaterials in an easy, safe, and reproducible way, superior to all other methods concerning flexibility with respect to the material. The method does not only work with the conducting elements one finds in the periodic table but also with the myriad of possible mixtures between them. For example, a mixture can be obtained by using different materials for the two electrodes.
We realized that this spark ablation device is a very useful source with incredible benefits: you can produce clean, controllable nanoparticles of any (semi)conducting material. These can be used as building blocks in nanotechnology, i.e., for producing nanomaterials or devices making use of assemblies of parts with very small dimensions. This is what we wanted people to do, and the number of these people in research and companies is rising.
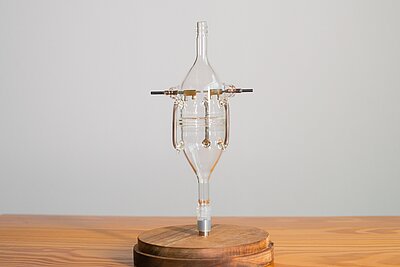
What about challenges at a scientific level? Did you have to convince researchers that this method works?
You always need to convince people when you come up with something new. The most challenging sector is catalysis because it is very delicate in the sense that small changes in the catalyst, e.g., induced by traces of contaminants, can disturb the catalytic process. Industries that have found a safe catalyst production process, into which they have invested a lot of effort, tend to hold on to it. As long as their process works, even our promise of purity and the ease of improving the catalyst by adding (mixing in) other components will not easily convince them to favour ours. In principle, our method's generic aspect allows people to make any catalyst. With the VSPARTICLE technology, you could, in theory, make catalysts with more than a trillion materials, because the spark ablation process allows you to mix all the (semi)conductor elements on the periodic table! The challenge for researchers is finding the best one for their application!
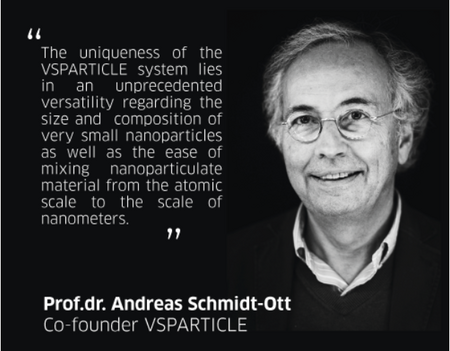
What are the applications of this innovative technology and its notable contribution?
Catalysis and chemical sensors (noses for specific chemicals) are today's most straightforward application areas. For example, particles from our spark ablation process have been shown to be very efficient as a catalysts in many examples.They are easily produced and exhibit more active surface than catalysts presently applied. In my opinion, one of the next steps to take should be a further improvement by mixing in other metals.
Using the feature of easily mixing materials that our technology offers us, we could use spark ablation to produce a material that has never been produced before every minute. We could then add a fast analysis process testing the material in view of a specific application, for example the catalytic behaviour for a specific reaction. This way, we will discover new materials by trial and error. If we add educated guesses, chemical simulations, and artificial intelligence, the discovery process will be accelerated enormously. The generic aspect of the VSPARTICLE approach, “mixing anything with anything”, is the key to improving catalysts and optimizing and discovering new materials for a large variety of applications, including storage of electrical energy and solar panels. This is important, in particular for a sustainable CO2-free future. Developing systems of higher energy efficiency and reducing, ultimately avoiding, the use of scarce materials (by mixing abundant ones!) are necessary objectives we can strongly contribute to.

Comments
No Comments