Previously published on Azonano Magazine
By Maurits Boeije, Material Scientist
Heterogeneous catalysis is at the nucleus of modern energy and chemical industries, a process in which a gas- or liquid-phase reaction is performed over a solid catalyst. Evidenced by revenue that reaches the trillions of dollars per year.To reduce our footprint on the earth and enter a new era where advances in technology are used to achieve this, conventional techniques processes that are typically more than fifty years old should be carefully reviewed.
Therefore, we turn our attention to catalyst preparation. A catalyst material consists of a host material (porous support) and active sites in the form of nanoparticles. The porous support functions as a template on which the particles are affixed. While wet-chemical methods and, more recently, gas-based methods are used for synthesis, many different methods have been developed to produce such materials over the years.
The Future of Heterogeneous Catalyst
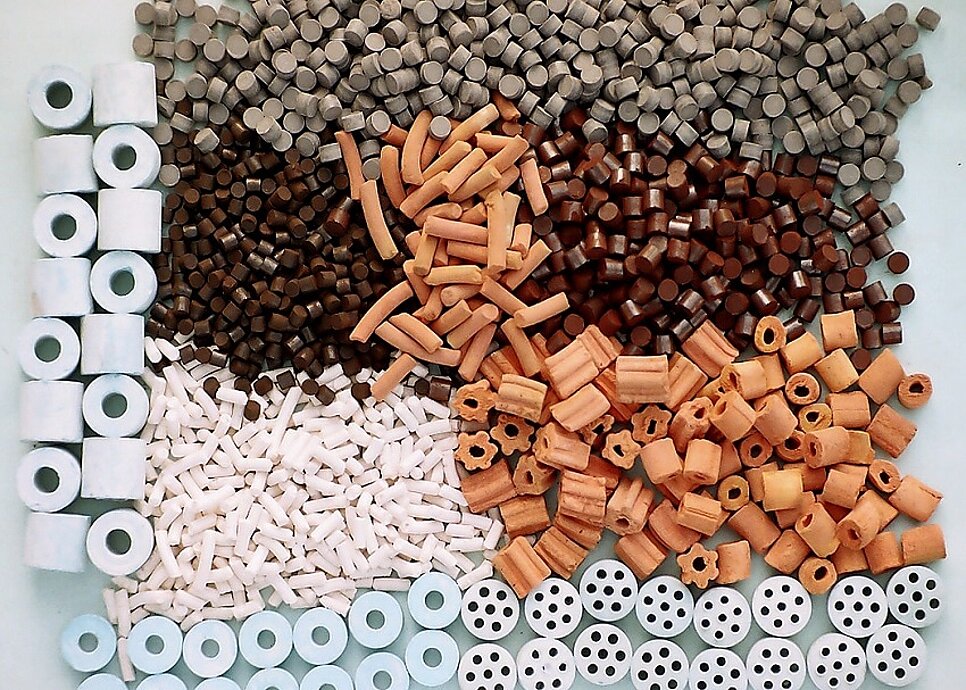
Wet Chemical Methods
Frequently used techniques in the industry rely on precipitation or impregnation. Sharing the commonality that the porous support is exposed to metal salt solutions, these methods introduce metal atoms into the pores of the material. The next requirement is a step where these metal atoms aggregate into nanoparticles. Finally, the impurities introduced in the previous steps are removed.
Precipitation techniques stimulate metal particle growth by supersaturation of the precursor solution, a process which culminates in nucleation and the growth of metal particles which can happen in conjunction with the formation of the support (coprecipitation) or on existing support (deposition precipitation). Impregnation techniques can act as alternatives as two main methods are distinguished, specifically, wet impregnation, which uses excess amounts of solution, and pore volume impregnation, in which a limited amount is used to just fill the pore volume of the support.
Current Limitations
These procedures are seemingly simple when explained in a general way, but precipitation and impregnation techniques take a lot of effort to combine the nanoparticle framework, necessary loading, size and distribution onto specific support. The loading is contingent on the overall starting concentration that is present in the pores and is a factor of limitation when using impregnation methods.
The resulting interplay is a complicated interplay between the solvent, the substrate, and the desired nanoparticle material, predominantly when adsorption plays an important role. The driving force for growth for which the nanoparticle size is dependent can be controlled by pH or temperature.
Throughout the sample, it is difficult to maintain a constant pH or temperature profile while also being difficult to reproduce. To complicate matters, the support can also be compromised in the process, notably when the pH is varied. Furthermore, residues of the anionic deposited require removal because they impact catalyst performance or even act as poisons. This is ordinarily achieved by a calcination step: oxidation brought about by high-temperature treatment of the air. Subsequently, the material can then be reduced in the next step when elemental metal nanoparticles are required.
Wet chemical synthesis methods are cheap to make in industrial quantities, making them established. The fact they have a lot of parameters to tune the catalyst creates a downside as these parameters are difficult to keep constant and this makes duplicating catalyst preparation and upscaling challenging. From an academic position, comparing the performance of the same catalyst that has been synthesized in various ways can be extremely complex. Preferably, one would only want to play with the support, particle size, and composition without having to adjust the recipe. This is where gas-based methods can prove to be useful.
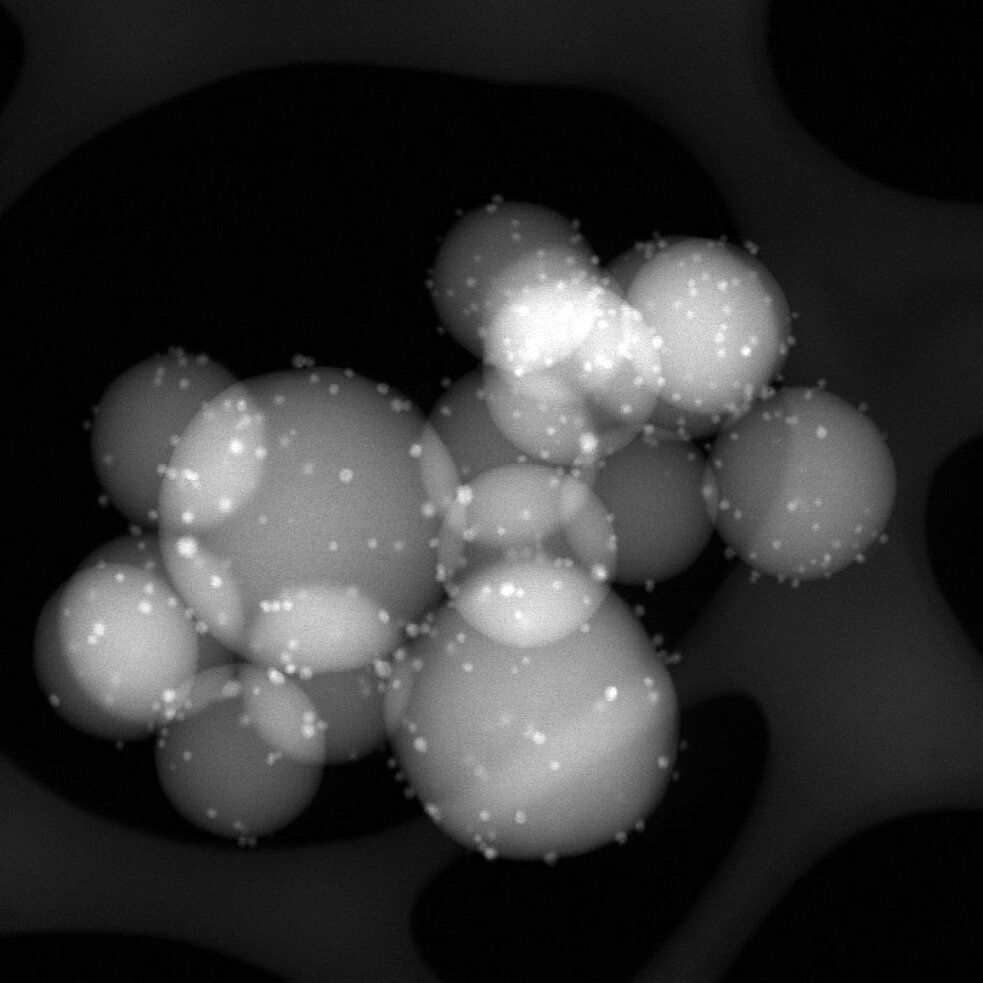
Comparison with Gas-Based Methods
Gas-based synthesis techniques, such as spark ablation, set apart nanoparticle synthesis from deposition. This way, the properties and loading can be tuned autonomously as there is no influence of the support on nanoparticle formation. This contrasts with the aforementioned methods as the nanoparticle growth is external to the pores of the support.
Porous bulk supports, like zeolites, cannot be used in this context because the nanoparticles do not reach far into the pores, but finely dispersed powders or thin porous membranes can be used. Moreover, because the starting material is a solid bulk alloy, the composition can be varied independently. By bringing the materials into a gas state, they can be carried by an inert carrier gas and develop from atomic clusters into spherical particles below 5 nm. The polydisperse output can be turned into a monodisperse output through filtering.
Modifications can be made by combining different vapors to produce core-shell particles or use oxygen in the carrier gas to make oxides.Taking place by diffusion and van der Waals forces, deposition gives rise to a weak, substrate independent interaction. The nanoparticle-support interaction can be improved in a later post-treatment step.
The Way Forward
By investigating the parameter space of material, size, loading and support for the most relevant reactions could ensure significant progress in the field of catalysis in the coming years. This should be executed in a way that is scalable and reproducible. Current samples are produced by methods that are difficult to compare and are not flexible enough to achieve this goal within a reasonable time. Gas-based methods can have a huge impact because of their flexibility and reproducibility and should be the way forward.
Comments
No Comments